Categories: Decontamination, Preservation & Stabilization, Client Support Services, Preventive Maintenance, Emergency Response
Equipment is designed to weather environmental conditions as specified by the original equipment manufacturer (OEM). While not an exhaustive list, such conditions may include relative humidity, temperature, temperature fluctuations, pressure, vibration, submersion and radiation. While some enclosed equipment, such as pad mounted transformers, generators, and electric meters can endure a great deal, a substantial amount of equipment is actually quite sensitive to deviation from specified environmental requirements.
When considering a post loss event, it is critical to understand what the equipment was designed to environmentally withstand, in order to determine the correct recovery options that would mitigate potential damage. This means that technical recovery may not be an option if the equipment was never designed to be submerged, or perhaps the environment, post loss, may not have deviated from what the equipment could endure, and technical decontamination would then be a favorable option as part of a comprehensive recovery.
This blog will provide a deep dive into restoration considerations, to ensure that the right recommendations are conveyed, and decontamination processes are not viewed as an environment outside of the OEM’s design requirements.
Quantifying Visible and Invisible Matter
Visual evaluation should be the first step in the overall equipment assessment process. If corrosive contaminants were introduced into the environment, and settled on sensitive metal assemblies or components, a visual observation may be sufficient to immediately determine that preservation activities should be employed to mitigate further damage.
While loss related contaminants are not always corrosive, their presence in between condensed circuit board components, could cause electrical signals to be rerouted via a short circuit. In many cases contaminants are somewhat invisible. This could be because the peril did not produce a significant amount of discolored debris, or that which was produced blended with pre-existing dirt. Therefore, analytically mapping contaminants in an effort to ascertain a migration pattern throughout the facility, is the second step in a thorough validation process.
When considering a validation process, remaining cognizant of what constitutes scientific proof or evidence is imperative. Evidence is considered scientific when it is either objective or repeatable. Some may perceive equipment restoration professionals as being subjective. Restoration professionals recommend recovery solutions, because it is a service they specialize in and offer.
The same folks perceive OEM account representatives as objective, because their recommendations may align with desired replacements, and if the OEM does not offer recovery as a service, such an option should not be considered. Therefore, repeatable scientific evidence is far more meaningful when quantifying the need and the success of equipment recovery. Repeatability means that results obtained by harvesting contamination samples, should be achieved with a high degree of agreement when replicated by other industry professionals.
Preservation and Stabilization
While quantifying contaminants scientifically instills certainty in the overall approach and subsequent recommendation, corrosive matter will require no introduction as it will cause fairly immediate deterioration on susceptible surfaces.
Preservation and stabilization activities help equipment owners minimize damage, and remain compliant with insurance policies that require active mitigation. One simply cannot allow equipment to deteriorate to the point where replacement is the only option. In some countries, fire fighters are required to call restoration professionals, in an effort to mitigate damage via preservation and insurance carriers pay for the service.
Preservation activities may include application of a rust inhibiting compound, such as ZEPRESERVE or WD-40, or a moisture-vapor barrier that can be employed on electronic components.
Decontamination Processes
Some companies offer their content recovery services like a restaurant buffet. There is a wide selection of services and they do their best to deliver a satisfactory result. In order to be able to realize a healthy return, such companies prefer automated cleaning processes, such as ultrasonic cleaners, versus employing human expertise. This begs the question, is one process suitable for any type of equipment?
Selecting the right decontamination processes requires a proper understanding of multiple variables:
- Equipment configuration and design. Will the proposed process affect any of the sensitive electronic or optical components? Or perhaps the polymeric film that was applied on some of the circuit boards?
- Components that are hermetically sealed, near-hermetic and non-hermetic. As an example, electronic plastic enclosure packages are non-hermetic. What would happen to internal components if these enclosures were submerged in an ultrasonic bath?
- Contaminants settled on a surface that is normally oiled, versus those that settled in a dry blade server computer. Would the same decontamination process apply regardless of how matted the contaminants are to the surface?
- The equipment owner, in this case an airport operator, provides a short time frame every night to complete the decontamination. After the last flight, or 1:00AM, and before the first flight, or 5:00AM. Does this mean one should consider an inferior decontamination method as a result of time constraints?
Therefore, depending on the type of equipment, a restoration expert will select the proper decontamination process. Consider a computer numerically controlled (CNC) 5-axis vertical machine center. The process employed on the tooling will not necessarily be the same as that which will be utilized on the control panel circuitry, or the non-technical surfaces within the machine (tool changer, spindle, table, ball screw).
- Dry Techniques - Suitable for post-loss technical recovery
- Modified Wet - Suitable for post-loss technical recovery
- Full Aqueous - Suitable for post-loss technical recovery / equipment dependent
- Batch Aqueous Cleaners | Defluxers - Suitable although equipment dependent
- Dry Ice Blasting - Suitable for post-loss technical recovery / equipment dependent
- Ultrasonic Cleaning - Not suitable for post-loss technical recovery of electronic circuitry. Suitable for machine tooling, hardware, rigid impermeable parts and composites.
Quality Assurance
Quality assurance involves a series of steps undertaken to ensure the deliverable meets client expectations and industry standards. Ensuring a successful recovery involves multiple specialists reviewing progression at set intervals, and collaborating with entities who have a vested interest via a warranty or service contract.
- Sample set of contaminants harvested via sterile pads and processed in a lab
- Equivalent salt density and conductance measurements
- Pre-disassembly peer audit
- Monitoring temperature and humidity during drying activities and maintaining real time continuous logs
- Post decontamination equivalent salt density and conductance measurements
- Sample set of contaminants harvested via sterile pads and processed in a lab
- Manufacture(s), as required by their recovery protocols, are given a copy of the sample lab results. This step ensures warranties and service contracts are not revoked.
- Post decontamination and re-assembly peer audit
- Strategic introduction of desiccant packs and corrosion control technologies
- Customer inspection of all deliverables, acceptance of work product and sign-off
Functional Testing, Repair and Recalibration
Technical recovery specialists can perform testing, repair, and recalibration on equipment in diverse industries. It benefits the equipment owner considerably more when their own service vendors, or in-house personnel, perform the functional portion of the recovery. Doing so instills a great deal of certainty. Those entities/personnel will have to service the equipment for years to come, and their first instinct should not be to attribute every wear and tear failure back to the loss event. Equipment will require normal preventive care, post loss, no different than the scheduled maintenance it was designed to receive.
Professional decontamination followed by testing, repair and recalibration, will provide the equipment owner the peace of mind necessary, to be able to continue operating their business as they did before the loss. The considerations outlined above are part of a methodical recovery process designed to ensure this peace of mind. If you experienced a fire or other disaster, contact us to find out how we can help you get back to business as quickly as possible.
ABOUT THE AUTHOR
By: Pedro Acevedo
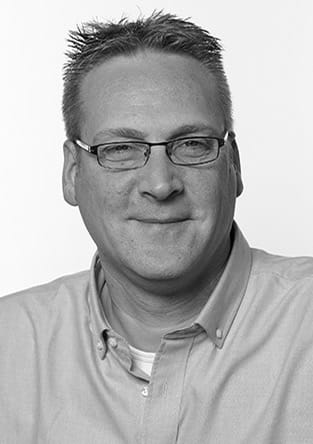
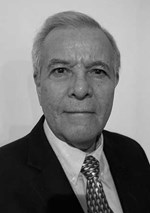
Pedro Acevedo is an electrical engineer with over 20 year experience in industrial design and maintenance in the fields of electrical, instrumentation, mechanical and automation. He’s lead planning and execution of major production plants overhauling and upgrading, being a direct beneficiary of valuable equipment restoration and care. His experience in corrosion control and coatings is an additional asset in understanding the phenomena present after machinery and equipment get exposed to catastrophes.